Why trusting Singho with your next casting project?
● 20 years of precision casting experience with an expert team.
● Proficient in CHINA, ASTM, ISO, EN, and JlS standards.
● Produces stainless steel, carbon steel, alloy steel, cast iron, copper, and aluminum/nickel alloys.
● Excels in high-standard, complex metal challenges, including low carbon/sulfur and high performance.
● High precision with accuracy from DCTG4 to DCTG6 and surface roughness Ra3.2 to Ra6.3
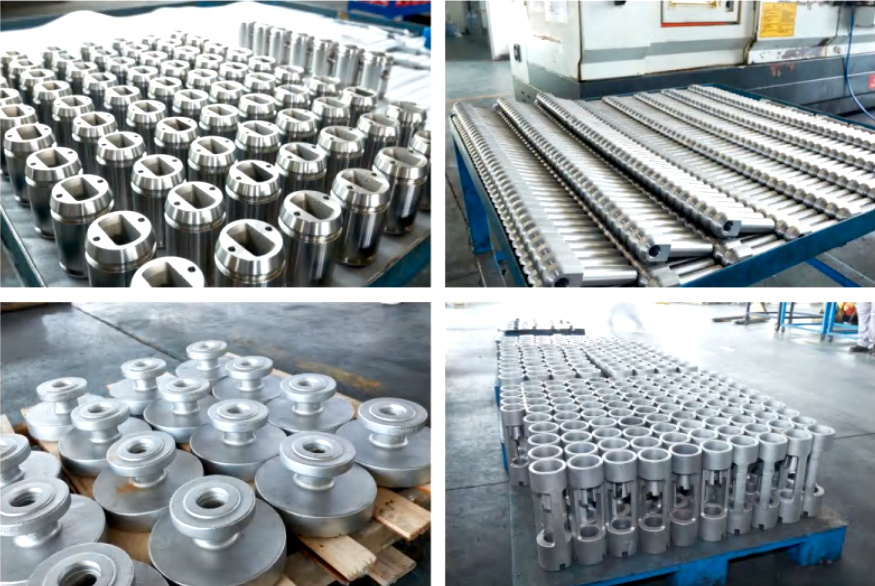
What is Investment Casting?
Investment casting is a precision metal casting process that delivers high-quality, complex components with intricate details and tight tolerances.
This capability can manage sudden increases in demand and is ideal for industries requiring precision and durability, such as oil and gas, automotive, marine, and more.
Why Choose Investment Casting?
Investment Casting is the smart choice for projects that demand metal parts with:
● Specialized alloys
● Incredibly tight tolerances
● Thin walls for reduced weight
● Impressive repeatability
● Less waste
● Reduced secondary operations
● Highly detailed surfaces and stamps
● Improved reputation for quality/return rate
● Reduced tooling costs over multiple production runs
A Look At Investment Casting Key Features
Key Features of our advanced investment casting machines include:
● Part weight range: a few ounces to 200+ pounds
● Parts range in size from the palm of your hand to a basketball
● Offers flexibility and design freedom
● Combines multiple complex parts into one casting
● Retains details of each combined part
● Flexibility to pour multiple alloys into one mold
● Minimizes stagnant inventory
Select Your Investment Casting Materials
Our wide range of compatible investment casting materials include:
● Carbon steel (e.g. AISI 1015 / 1045 / 1080)
● Alloy steel (e.g. AISI 4140 / 4340 / 8620)
● Stainless steel (e.g. 300 series, 400 series, 17-4PH, 15-5PH)
● Complex alloy (e.g. G22NiMoCr5-6)
● Aluminum
● Cobalt & Nickle based alloy
The Investment Casting Process
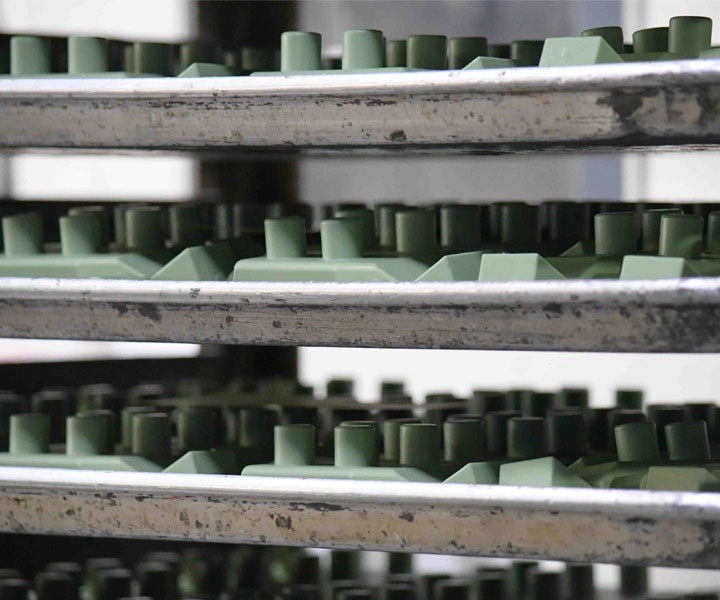
01
Cast Wax Pattern
The first step of the Investment Casting Process is to create a wax pattern of casting part by using high temperature wax injected into an aluminum molding tool.
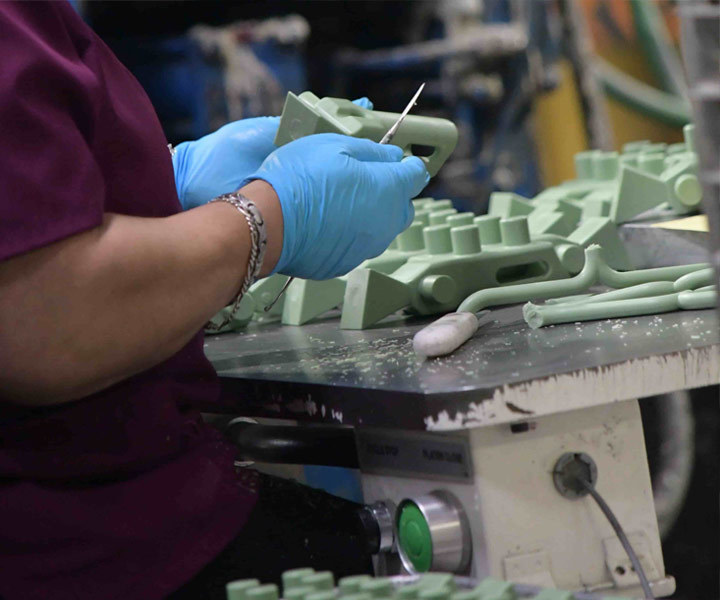
02
Assembly
The second step of the Investment Casting Process is to attach the wax models to a gate or system. From there, multiple patterns are assembled for large quantity production.
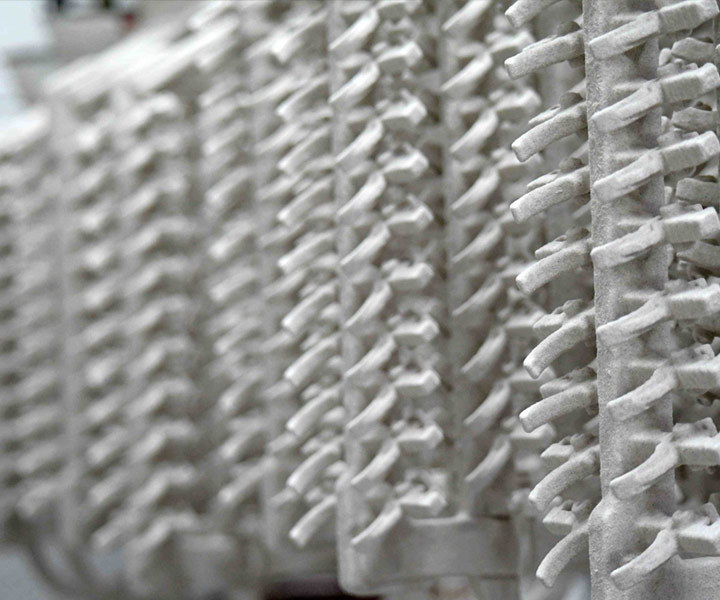
03
Shell Building
The third step of the Investment Casting Process is dipping the system into ceramic to build up layers to create thickness. The shell is typically 3/8" thick.
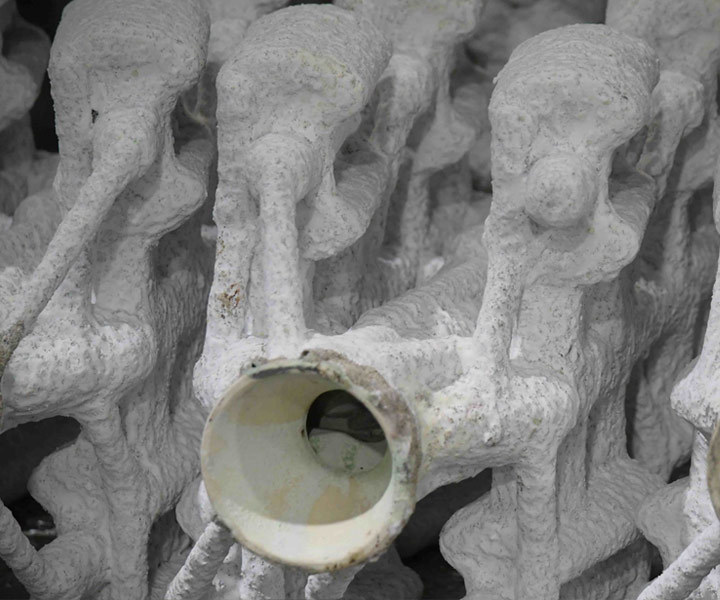
04
Dew axing
The fourth step of the Investment Casting Process requires melting the wax out of the cavity to leave a hollow ceramic outer layer.
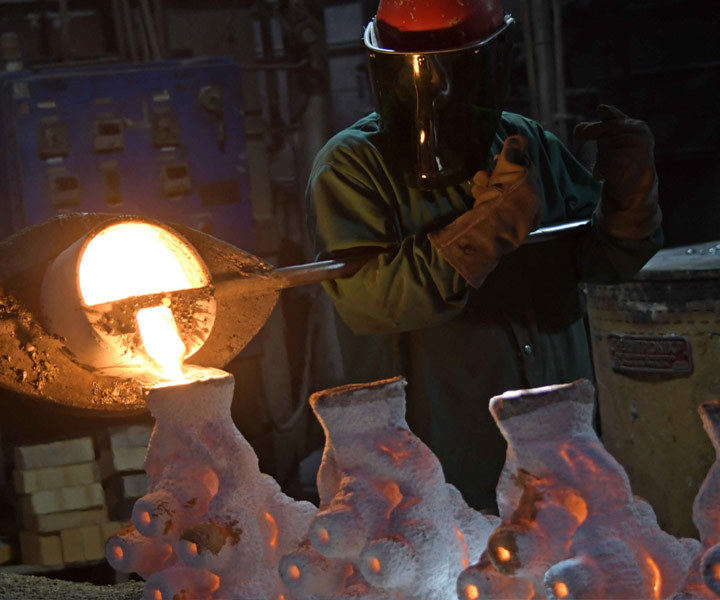
05
Pouring & Solidification
The fifth step of the Investment Casting Process involves heating the cavity, to prevent shock of the metal, and pouring the metal into the ceramic shell.
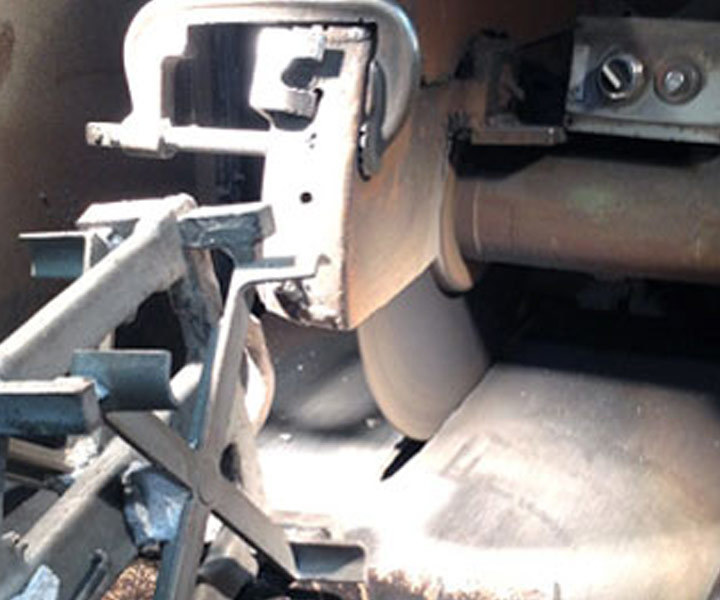
06
Sawing / Cutting
The sixth step of the Investment Casting Process is removing the casting from the runner system.

07
Customization
The seventh step of the process involves grinding the part until it meets specifications of the orginal part. Depending on tolerance & requisites, some additional heat treating & secondary machining may be required.
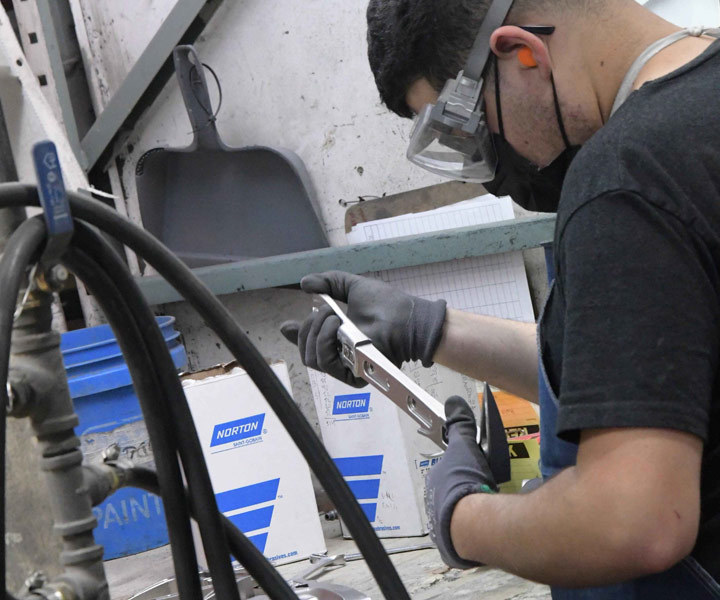
08
Finish
The eighth and final step of the Investment Casting Process is measuring and ensuring quality of the new part using advanced tools to make sure the new part is an exact duplication of the original casting.

01
Cast Wax Pattern

02
Assembly

03
Shell Building

04
Dew axing

05
Pouring & Solidification

06
Sawing / Cutting

07
Customization

08
Finish
Industry Solutions